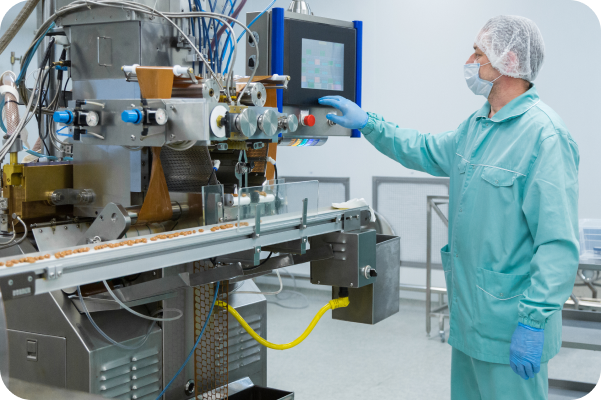
Safety and Quality:
Atharva Bio pharma manufacturing places utmost importance on safety and quality throughout the production process. Stringent regulatory standards, including Good Manufacturing Practices (GMP), are followed to guarantee the efficacy, purity, and safety of the final product. Rigorous quality control measures are implemented at every stage to monitor critical parameters, perform testing, and maintain consistent batch-to-batch quality.
State of Art Facility
Plot Area | 20000 sq. mtr |
---|---|
Manufacturing Facility | 3433 sq. mtr |
Dedicated Clean room | 765 sq. mtr |
QC/QA/Micro Laboratory facility | 578 sq.mtr |
R&D and P&D Laboratory | 272 sq.mtr |
Hydrogenation Facility | 144 sq.mtr |
PESO Tank Farm | 20 KL, 4 Tanks, Provisioned 2 Tanks |
ETP / MEE / STP ( ZLD ) area | 930 sq. mtr |
R.M. material Stores | 500 sq. mtr |
Solvent Drums Storage Facility | 500 sq. mtr |
Technical Expert Staff | |
Raw Material Facility | |
Switch yard / Transformer yard | 156 sq. mtr |
Security cabin / OHC center | 70 sq. mtr |
Packaging Number Storage Facility |
Utilities | Capacity |
---|---|
Transformer | 750 kVA 01 No. |
D.G. set | 750 kVA 01 No. |
Steam boiler ( IBR ), Solid fuel | 2500 kg/hr ( 2.5 TPH ) 01 No. |
Brine Chiller | 20 TR at-20 Deg.C 01 No. |
Cooling tower for process | 200 TR 02 No. |
Cooling tower for Utility Chiller | 60 TR 01 No. |
Cooling tower for MEE | 100 CFM 01 No. |
Nitrogen generation Plant | 10 NM3 /hr 01 No. |
Purified water generation & Distribution | 500 Ltr/hr 01 No. |
MIDC water storage tank | 250kl 01 No. |
Air Handling system for Microlab | 4000 CFM 01 No. |
Air Handling Unit for clean room | 5000 CFM 04 No. |
Manufacturing Facility | Capacity |
---|---|
Reaction capacity | 53.5 kL |
Glass lined reactor | 1000 litre 01 No. |
Glass lined reactor | 2000 litre 03 No. |
Glass lined reactor | 3000 litre 02 No. |
Glass lined reactor | 5000 litre 01 No. |
S.S. 316 reactor | 1000 litre 03 No. |
S.S. 316 reactor | 2000 litre 04 No. |
S.S. 316 reactor | 3000 litre 03 No. |
S.S. 316 reactor | 4000 litre 02 No. |
S.S. 316 reactor | 5000 litre 01 No. |
S.S. 316 Hydrogenator | 1500 litre 01 No. |
S.S. 316 Hydrogenator | 100 litre 01 No. |
S.S. 316 Centrifuges | 48" 02 No. |
S.S. 316 Centrifuges | 36" 02 No. |
S.S. 316 with antistatic halar coated centrifuges | 36" 02 No. |
S.S. 316 Air Tray Dryers,steam heated | 48 trays 02 No. |
VTD ( vacuum tray dryer ) | 12 trays 01 No. |
Octagonal Blender | 500 Liter 01 No. |
Double cone Blender | 300 Liter 01 No. |
Milling ( Multi Mill ) | 200 kg/hr 02 No. |
Vibro Sifter | 36" 02 No. |
Powder Processing area | ISO 8 ,Grade D 02 No. |
Scrubber System | 2000 CFM 01 No. |
Good Lift | 2 Ton 01 No. |
S.S. 316 addition tanks | 500 Liter 04 No. |
S.S. 316 addition tanks | 250 Liter 06 No. |
S.S. 316 Zero Hold up Sparkler Filter Press | 18 x 15 plates 01 No. |
S.S. 316 Zero Hold up Sparkler Filter Press | 18 x 10 plates 01 No. |
RCVD ( Rotocone vacuum dryer ) | 300 litre 01 No. |
Quality Control Lab | Capacity |
---|---|
HPLC | 0 02 No. |
GC | 0 02 No. |
Microlab facility with incubator, autoclave, LAF etc. | 0 01 No. |
R & D Lab | Capacity |
---|---|
Fume Hoods | 1800 mm 02 No. |
Glass assembly | 10 Liter 02 No. |
Glass assembly | 5 Liter 02 No. |
Glass assembly | 2 Liter 02 No. |
Lab Autoclave | 10 L Capacity 01 No. |
Rota Evaporate assembly | 10 L 01 No. |
Rota Evaporate assembly | 2 L 01 No. |
Fire Hydrant system | Capacity |
---|---|
Fire water tank | 200 kL 01 No. |
Hydrant pump | 175 cu.m/hr 02 No. |
Diesel pump | 175 cu.m/hr 01 No. |
Jokkey pump | 10 cu.m./hr 02 No. |
ZLD Effluent Treatment Facility | Capacity |
---|---|
MEE ( Multi Effect Evaporator ) for High COD effluent | 30 kLD 01 No. |
ETP ( Biological Treatment for Low COD) | 40 kLD 01 No. |
R.O. plant | 25 kLD 01 No. |
STP | 10 kLD |
Raw Material Stores | Capacity |
---|---|
Solvent Storage tanks for Petroleum A class solvents | 20 kL 02 No. |
Fresh solvent Day tanks | 5 kL 02 No. |
Solid raw material stores | 5000 sq. ft. 01 No. |
Liquid Stores / Drum Storage area | 3000 sq. ft. 01 No. |
Dispensing & sampling booth | ISO 8, grade D 02 No. |